Major Problems and Solutions On Industrial Concrete Pumping
What are the main problems in the use of industrial concrete pumps, and how can we solve these problems?
In fact, industrial concrete pumps, also known as concrete delivery pumps or concrete boom pump trucks, are all construction machinery and equipment with a high degree integration of electronic system, mechanical system and hydraulic system.
Among them, open type and close type are two common modes of hydraulic system.
The distribution valve includes rotary valve, gate valve, S-shaped valve, etc.
The electrical controlling system with PLC programmable controller, provides stable and reliable performance.
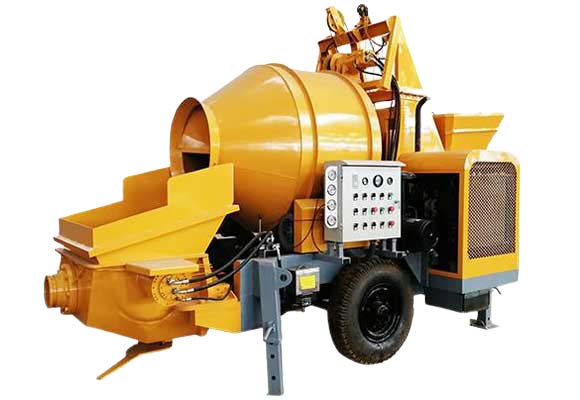
In terms of machinery, no matter what kind of pumping equipment it is, its executive elements all include the main delivery hydraulic oil cylinder, the distribution valve swing cylinder and the mixing motor.
Among them, the direction transferring of the oil cylinder is controlled by the limit switch (or proximity switch) of the corresponding solenoid valve.
Once the pump body fails at work, it is usually checked first from the three aspects of mechanism, hydraulics and electrics.
The rotating speed of the main power engine cannot reach the rated value.
When press the start button of the main motor, the motor can run, but can not reach the rated speed. And when the connection is changed from star mode connection to delta mode connection, the motor stops automatically.
When encountering such problems, first check whether the power supply voltage is normal and whether the transformer capacity is sufficient (transformer capacity is generally 1.15 times the calculated load).
Then measure the starting voltage and calculate whether the wire diameter of the power supply line meets the requirements.
And ensure that the line voltage drop is within the specified range (the allowable value of the line voltage drop is generally not greater than 5%). If the drop of the starting voltage is too large, the wire diameter can be appropriately increased.
In addition, improper operation and failure of the hydraulic system can also cause difficulty in starting. So, before starting the machine, you should first check whether the operating handles of the water pump and the mixing motor are in the neutral position, and whether the pumping button is turned off.
If it still cannot be started, check whether the solenoid valve that controls the pressure of the fuel injection pump is normal, and ensure that the main oil pump is in the unloaded state when starting.
When press the pumping button, the concrete delivery cylinder does not work or works weakly.
1.Check whether the hydraulic oil level is normal. If it is insufficient, add it to the specified position. Restart the motor and observe whether the reading of the vacuum gauge is within the normal range to determine whether the filter needs to be replaced.
2.In the shutdown state, turn on the main power, press the pumping button, and carefully check whether the solenoid valve that controls the pumping is working.
You can also use a multimeter to measure the on-off status of each relevant solenoid valve. If it is not normal, it should be further determined. Or the solenoid valve coil is damaged or the spool is stuck. If it is normal, check the action of the hydraulic reversing valve.
3.If the main oil cylinder does not move in the reversing position, it is most likely that there is a problem with the limit switch.
4.Check the pressure of the main pump system (during pumping operation). If it does not reach the specified value, check the relief valve and the main oil pump.
For a closed system, under normal circumstances, the motor starts and the charge pump works, and the pressure display should be around 2.5MPa.
If the pressure is insufficient, adjust the safety valve of the charge pump and check the wear of the charge pump.
5.The temperature of the hydraulic oil is too high, resulting in increased leakage, a drop in oil pressure, and inability to work. The cooling system should be overhauled to ensure good cooling effect.
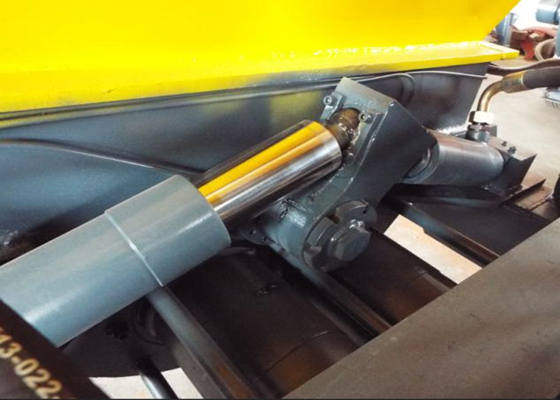
Common failures and solutions of the reversing system
Main Oil Cylinder Not Work
Table1 Main oil cylinder reversing-failure reasons and solutions
Failure Reasons | Solutions |
Lack of Hydraulic Oil | Fill hydraulic oil to the specified level |
Blown Fuse | Replace the fuse |
Bad contact on the reverse button | Repair or replace the reverse button |
Reverse relay socket wiring is loose | Eliminate loose wiring |
Damaged delay relay in electrical control box | Replace the delay relay |
LEDs do not flash | Replace the LEDs |
LEDs are always on | Tighten the switch |
Hydraulic reversing valve spool sticks due to dirt | Remove dirt from the reversing valve spool and make the spool to move freely |
Solenoid reversing valve coil blown | Repair or replace solenoid valve |
Distribution Valve Cannot Reverse Automatically
Table2 Distributing Valve Reversing Fault Causes And Troubleshooting Methods
Failure Reasons | Solutions |
The accumulator oil circuit is not charged. | Check the accumulator pressure, close the accumulator unloading valve. |
Dispense valve reverse switch damaged or bad contact | Repair or replace the reverse switch. |
Aggregate is accumulated in the swing area of the S tube or the aggregate is deposited in the hopper, which hinders the reversal. | 1.The aggregate in the S-tube area is pumped out by means of repeated reversal and reverse pumping. 2.If necessary, the discharge outlet of the hopper can be opened to remove the aggregate deposits. 3.The pumped concrete should meet the pumpability requirements. |
The Distribution Valve Swings Weakly
The weak swing of the distribution valve is generally caused by insufficient oil pressure, and the reason for insufficient oil pressure is abnormal leakage. The specific inspection steps are as follows:
1. Check the appearance to see if there is any leakage of oil pipes, joints, valve bodies, oil pumps and oil cylinders.
2.Check whether the oil level of the hydraulic oil is normal and whether the oil inlet filter element is too dirty, otherwise it may cause poor oil intake.
Under normal circumstances, the blockage of the filter element will be accompanied by increased noise and increased oil temperature, and the reversing pressure is insufficient, sometimes not, so it should be replaced in time, otherwise it will accelerate the wear of the oil pump and other hydraulic components.
3.Adjust the overflow valve to see if the pressure rises. If it does not rise, check the overflow valve to see if the spring is damaged or stuck, and whether the valve body is seriously worn.
4.Check the accumulator pressure. It can be checked with a pressure gauge when the machine is stopped, generally 110MPa. It can also be judged by observing the drop of the pressure gauge reading when the machine is running.
Under normal circumstances, the pressure drops by 3MPa to 4MPa during reversing. If it does not meet the specified value, store energy. The bladder may be damaged and needs to be replaced.
5.Check whether the distribution valve is strained or severely worn, resulting in insufficient pressure.
6.For the distribution system with a constant flow pump (some concrete delivery pump distribution systems and the main cylinder share an oil pump).
After completing the above steps, you should also check whether the pressure of the pump is normal. If the pressure is insufficient, adjust or dismantle its wear condition.